In the electronics manufacturing industry, SMT (Surface Mount Technology) and through-hole soldering are two common surface assembly techniques. While both are methods for soldering electronic components, they exhibit notable differences in processes and applications. This article will explore the distinctions between SMT processing and soldering techniques to help readers better
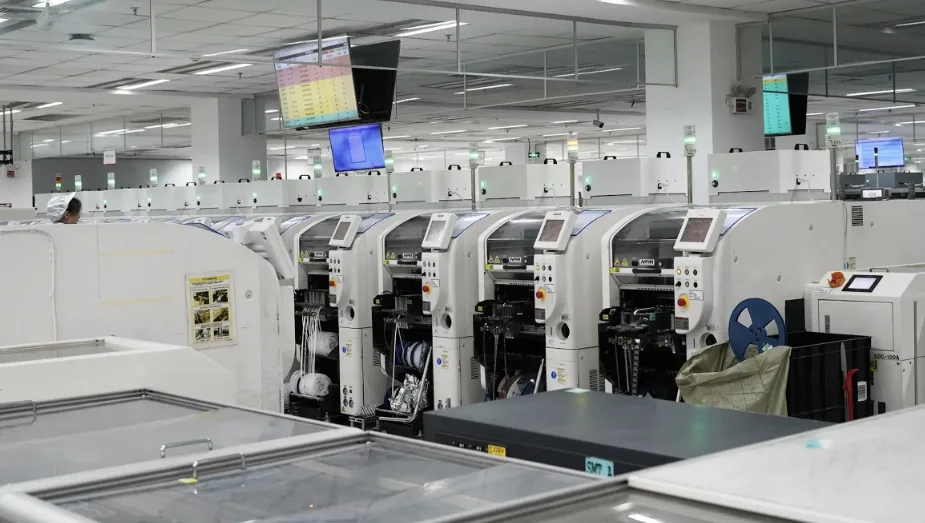
In the electronics manufacturing industry, SMT (Surface Mount Technology) and through-hole soldering are two common surface assembly techniques. While both are methods for soldering electronic components, they exhibit notable differences in processes and applications. This article will explore the distinctions between SMT processing and soldering techniques to help readers better understand their differences and suitable use cases.
SMT Processing
SMT, or Surface Mount Technology, is a method of directly mounting electronic components onto a PCB (Printed Circuit Board). By soldering components onto the pads on the PCB’s surface, it achieves the connection and assembly of electronic devices.
Compared to traditional through-hole technology, SMT offers higher integration, smaller size, and lower costs. SMT manufacturers use automated equipment to place electronic components directly onto the PCB surface, bonding them with molten solder. This technology is widely applied in electronics such as smartphones, tablets, and televisions, and plays a vital role in miniaturization, lightweight designs, and high-frequency applications.
Advantages of SMT
- High Assembly Density:
SMT processing significantly increases the assembly density of electronic products. The compact size and short or leadless pins of surface-mount components allow them to be tightly arranged on PCBs, conserving space and reducing product size.
- Lightweight Design:
By employing miniaturized components, SMT-produced products are lighter than those using traditional through-hole components. This is particularly important for weight-sensitive products such as portable devices and aerospace electronics.
- High Reliability:
SMT ensures high soldering quality with low defect rates. Components are directly mounted on the PCB surface and soldered using processes like reflow soldering, resulting in more robust solder joints and reducing failures caused by poor contact or defective soldering.
- Ease of Automation:
The SMT process is highly automated, from component placement to soldering, which enhances production efficiency and minimizes human error, improving overall product quality.
- Improved Production Efficiency:
Automated production lines enable SMT processing to complete large-scale manufacturing quickly. Since component placement and soldering occur simultaneously, production delays are minimized, resulting in greater efficiency.
Post-Soldering Technology
Post-soldering is a process in which pre-assembled electronic components on a PCB are heated in a reflow oven to melt the solder and complete the connections. It is commonly used in the production of double-sided or multilayer boards. The primary advantages of post-soldering include high soldering strength, low contact resistance, and compatibility with larger or higher-power components. During post-soldering, assembled components are placed in a reflow oven, where temperature and time are carefully controlled to achieve the desired soldering quality. After soldering, reliability testing is conducted to ensure that the quality meets required standards.
Advantages of Post-Soldering
- Enhanced Production Flexibility:
Post-soldering allows engineers to adjust component layouts on circuit boards according to actual needs, accommodating changes in product performance, functionality, or cost requirements.
- Reduced Production Costs:
In the initial soldering stages, defects may occur for various reasons. Post-soldering enables targeted repairs of problem areas without requiring the removal of the entire circuit board. This reduces material waste and production costs.
- Improved Product Quality:
Through meticulous post-soldering operations, the soldering quality of each component on the circuit board can be ensured, enhancing the reliability and stability of the final product.
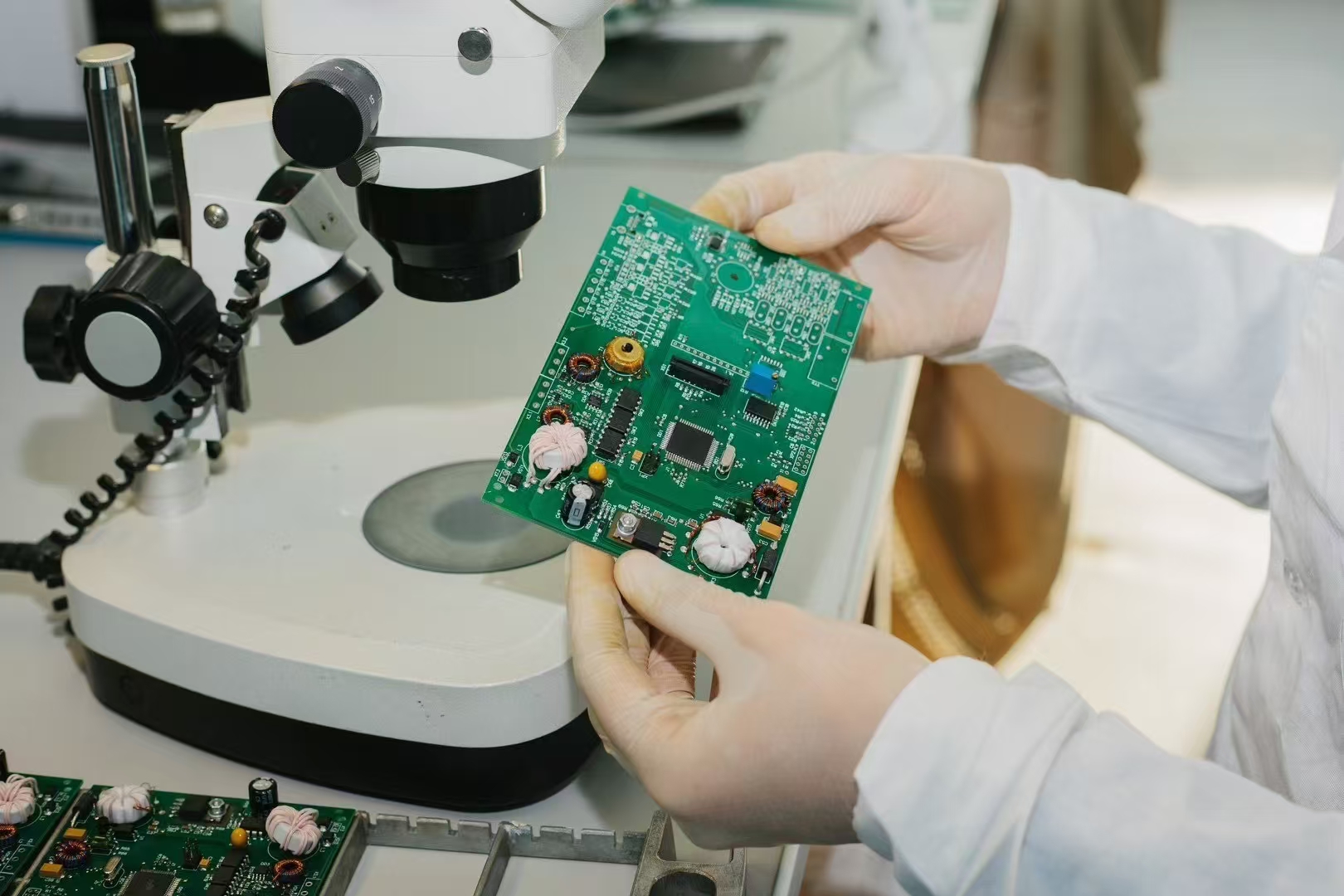
Differences Between SMT and Post-Soldering
SMT (Surface Mount Technology) and post-soldering are two commonly used surface assembly techniques in the electronics manufacturing industry. They differ significantly in process, application, and characteristics. Below is a detailed comparison:
1. Process Differences
SMT:
- Involves directly mounting electronic components onto the surface of a PCB (Printed Circuit Board).
- Utilizes automated equipment to place components on the PCB surface, bonding them with molten solder.
- SMT processes can be divided into solder paste reflow soldering and adhesive wave soldering methods.
Post-Soldering:
- A process that uses a reflow oven to heat pre-assembled electronic components on a PCB, melting the solder to complete the connections.
- Requires pre-assembled components to be placed in a reflow oven, where temperature and time are controlled for soldering.
- Often follows SMT processes to handle components that cannot be processed using SMT alone.
2. Application Differences
SMT:
- Widely used in electronic products such as smartphones, tablets, and televisions.
- Suitable for miniaturized, lightweight, and high-frequency applications.
- Enables high integration, making it ideal for manufacturing high-performance electronic products.
Post-Soldering:
- Commonly employed in the production of double-sided or multilayer PCBs.
- Suitable for assembling larger components and PCBs, such as power circuits and amplifiers.
- In some special applications, post-soldering is used to enhance soldering reliability or address unique component requirements.
3. Characteristic Differences
SMT:
- Offers higher integration, smaller component sizes, and lower costs.
- Highly automated, providing high production efficiency while reducing labor and material costs.
- Ensures high reliability, excellent shock resistance, low defect rates, and superior high-frequency characteristics.
Post-Soldering:
- Provides high soldering strength and low contact resistance.
- Accommodates larger and higher-power components.
- Involves more complex operations, requiring additional manual intervention but delivering high soldering reliability.
Conclusion
SMT and post-soldering differ significantly in process, application, and characteristics. The choice between these technologies depends on specific application needs, product requirements, and production conditions. In practical applications, selecting the appropriate soldering method based on product features and production demands can improve efficiency and ensure product quality.